Снижение механических потерь в автотракторных ДВС.
Текст напечатан в сокращенном виде с комментариями. [ 20.09.02 г.] |
|
Автореферат, док. Наук. Москва, 1997 г. УДК 621.43-242-2431.
|
Путинцев С.В.
|
Обзор источников механических потерь.
Из анализа потерь энергии в ДВС следует, что в нынешнее время, когда уровень индикаторных показателей форсированных ДВС близок к предельному, дальнейшее улучшение топливной экономичности необходимо связывать с увеличением эффективности работы за счет снижения потерь механической энергии, затрат на трение, износ и соударение деталей.
45 % – 60 % потерь в ЦПГ. Следовательно есть резервы. У нас отставание по таким вопросам, как трение, механический КПД, масла, т.е. тем, что напрямую связано с тиботехническими процессами в ЦПГ ДВС. Отсутствие научно обоснованного подбора материалов и смазок, уменьшающих потери.
Применение материалов с низким коэффициентом трения :
мех. потери на 4-10; топливо – 1-3%; уменьшение износостой.
Переход на маловязкие масла и присадки:
мех. потери на 8-20; топливо на 2-5%; агрессив. Присадок к цв. Мет.
Рациональное профилирование поверхностей трения:
мех. потери на 10-25; топливо на 3-6%; ограничений нет.
Режим смазки колец – смешанный и граничный в зоне смены знака скорости, с переходом на гидродинамическое в зонах с максимальной скоростью. Режим смазки поршня – преимущественно гидродинамический с небольшими участками граничного и смешанного трения в зоне действия максимальных опрокидывающих моментов.
Трение колец зависит то нагрузки (давления газа и упругости колец); а поршня от температуры (т.е. вязкости масла) и скоростного режима ДВС. Минимальные энергетические потери достигаются на максимальной гидродинамической несущей способности движущихся деталей. На данную составляющую влияет форма профиля поршня и форма микро профиля. Вес поршня должен находиться в районе пальца. Конструкционные материалы должны быть с минимальным коэффициентом трения. Согласование геометрии торцевой поверхности с формой канавки поршня.
В некоторых случаях получается эффект синергизма – от удачного сочетания качества масла и модификатора трения взаимное резкое улучшение смазочных и фрикционных свойств.
Как пример приводится композиции Фоспол, Фриктол (НПО "Масла", г. Киев) для дизельных (снижение до 30% с коэффициентом 0,085) и для карбюраторных "Аспект модификатор" г. Москва (снижение до 10% с коэфф. 0,112).
Материалы – (композит карбида кремния) Al 30 + 20% SiC (f = 0.09) – материал поршней. Кольца - Графелон 920 (f = 0,105). Если нельзя изменить конструкцию, материалы, технологию изготовления остаются смазки и присадки.
Обычно не учитывается форма цилиндра. Возможно уменьшение диаметра в верхней части по закону увеличения давления и некоторое увеличение в средней части по стандартам цилиндра. Т.к. в средней части гидродинамическое трение и высокая скорость. Верхняя часть цилиндра упрочняется и обрабатывается с уменьшением диаметра. Уменьшение можно достичь за счет напыления. Дается возможность кольцам двигаться в канавках, до минимального размера в стиле кольца.
Для увеличения толщины слоя твердой смазки диаметр поршня в масле должен быть меньше 2 – 3 мКр не влияет на смазочный клин и на образование клина в верхней части.
Принцип трибоадаптивности нашел отражение в конструкции опытных поршней: бочкообразных с центрально – симметричной юбкой; бочкообразных с переменным профилем и микрорельефом; 2х опорных с термоадаптивной юбкой, имеющих трапециевидные несущие участки и поршни с асимметричной канавкой под установку верхнего компрессионного кольца. Можно сделать следующие выводы: профилированием юбок поршней; применением антифрикционных материалов для поршневых колец; использованием смазочных композиций можно достичь снижения потерь на трение до 11 – 13 % и следовательно потерь топлива на 6 – 12 гр./квт час (2,5 – 5 %).
Наиболее низкий удельный расход при 2000 –2200 об/мин.
|
Выводы и комментарии.
|
Оширов В.
|
Качество механической обработки поверхностей важно, как и форма. Это подтверждает эффективность применения твердых смазок для верхней части цилиндра.
|
Возврат в список
© Оширов В. 2002 г.
Главная страница
Статьи и разработки
Обсудить на форуме
E-mail: ingenerw@km.ru
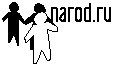
|